Blaasgieten is een veelgebruikt productieproces voor het maken van holle kunststof onderdelen. Het is vooral populair bij de productie van containers, flessen en diverse andere producten. De kern van het blaasvormproces is deblaasvormmachine, dat een cruciale rol speelt bij het vormen van het plastic materiaal tot het gewenste product. In dit artikel zullen we kijken naar de vier fasen van blaasgieten en hoe een blaasvormmachine elke fase vergemakkelijkt.
Voordat we ons verdiepen in elke fase, is het noodzakelijk om te begrijpen wat blaasgieten is.Blaasvormenis een productieproces waarbij een verwarmde plastic buis (een parison genoemd) in een mal wordt geblazen om een hol voorwerp te vormen. Het proces is efficiënt en betaalbaar, waardoor het een populaire keuze is voor de productie van grote hoeveelheden kunststofproducten.
De vier fasen van blaasgieten:
Blaasgieten kan worden onderverdeeld in vier verschillende fasen: extrusie, vorming, koeling en uitwerpen. Elke fase is van cruciaal belang voor het algehele succes van het blaasvormproces, en blaasvormmachines vergemakkelijken elke fase.
1. Extrusie
De eerste fase van het blaasgieten is extrusie, waarbij plastic pellets in een blaasvormmachine worden gevoerd. Deblaasvormmachineverwarmt de plastic pellets totdat ze smelten en vormt een continue buis van gesmolten plastic, een parison genaamd. Het extrusieproces is van cruciaal belang omdat het de dikte en uniformiteit van de parison bepaalt, wat rechtstreeks van invloed is op de kwaliteit van het eindproduct.
In dit stadium gebruikt de blaasvormmachine een schroef of plunjer om het gesmolten plastic in de mal te duwen om de parison te vormen. Temperatuur en druk moeten zorgvuldig worden gecontroleerd om ervoor te zorgen dat het plastic volledig is gesmolten en in de volgende fasen gemakkelijk kan worden gevormd.
2. Vorming
Zodra de parison is gevormd, wordt de vormfase ingegaan. In deze fase wordt de glasklomp in de mal geklemd om het eindproduct vorm te geven. De blaasvormmachine brengt vervolgens lucht in de parison, waardoor deze uitzet totdat deze de mal volledig vult. Dit proces staat bekend als blaasvormen.
Het ontwerp van de mal is van cruciaal belang omdat het de uiteindelijke maat en oppervlakteafwerking van het product bepaalt. In dit stadium moet de blaasvormmachine de luchtdruk en temperatuur nauwkeurig regelen om ervoor te zorgen dat de parison gelijkmatig uitzet en zich aan de wanden van de mal hecht.
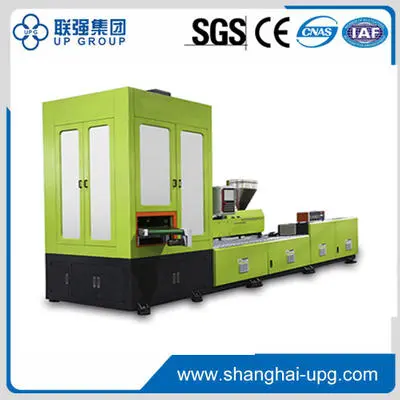
1. Het model uit de AS-serie maakt gebruik van een structuur met drie stations en is geschikt voor de productie van plastic containers zoals PET, PETG, enz. Het wordt voornamelijk gebruikt in verpakkingscontainers voor cosmetica, farmaceutische producten, enz.
2. De spuitgiettechnologie bestaat uit machines, matrijzen, vormprocessen, enz. Liuzhou Jingye Machinery Co., Ltd. onderzoekt en ontwikkelt deze technologie al meer dan tien jaar.
3. Onze injectie-rek-blaasvormmachine heeft drie stations: injectievoorvorm, strentch & blow en uitwerpen.
4. Dit proces in één fase kan u veel energie besparen, omdat u de preforms niet opnieuw hoeft te verwarmen.
5. En kan ervoor zorgen dat de fles er beter uitziet, door te voorkomen dat voorvormen tegen elkaar krassen.
3. Koeling
Nadat de glasklomp is opgeblazen en gevormd, gaat deze de afkoelfase in. Deze fase is essentieel voor het uitharden van het plastic en ervoor zorgen dat het eindproduct zijn vorm behoudt.Blaasvormmachinesgebruik meestal koelkanalen of lucht om de temperatuur van het vormdeel te verlagen.
De afkoeltijd varieert afhankelijk van het gebruikte type kunststof en de dikte van het product. Een goede koeling is van cruciaal belang omdat dit de mechanische eigenschappen en de algehele kwaliteit van het eindproduct beïnvloedt. Als het koelproces niet goed wordt gecontroleerd, kan dit leiden tot kromtrekken of andere defecten in het eindproduct.
4. Uitwerpen
De laatste fase van het blaasgieten is het uitwerpen. Zodra het product is afgekoeld en gestold, wordt hetblaasvormmachineopent de mal om het eindproduct vrij te geven. Deze fase moet zorgvuldig worden uitgevoerd om schade aan het product te voorkomen. De machine kan een robotarm of uitwerppen gebruiken om te helpen bij het verwijderen van het onderdeel uit de mal.
Na het uitwerpen moet het product mogelijk nog andere verwerkingsstappen doorlopen, zoals afsnijden of inspectie, voordat het kan worden verpakt en verzonden. De efficiëntie van de uitwerpfase kan een aanzienlijke impact hebben op de totale productiecyclus en is daarom een cruciaal onderdeel van het blaasvormproces.
Blaasgieten is een efficiënt en veelzijdig productieproces dat afhankelijk is van de nauwkeurige werking van de blaasvormmachine. Door het begrijpen van de vier fasen van het blaasgieten (extrusie, vormen, koelen en uitwerpen) is het mogelijk inzicht te krijgen in de productie van holle kunststofproducten. Elke fase speelt een cruciale rol bij het waarborgen van de kwaliteit en consistentie van het eindproduct.
Nu de vraag naar hoogwaardige kunststofproducten in een breed scala van industrieën blijft groeien, wordt de vooruitgang in de sector steeds groterblaasvormentechnologie en machines zullen waarschijnlijk de efficiëntie en mogelijkheden van het blaasvormproces vergroten. Of u nu een fabrikant, ingenieur of gewoon geïnteresseerd bent in de wereld van de kunststofproductie, het begrijpen van deze fasen zal uw begrip van de complexiteit en innovatie achter blaasvormmachines verdiepen.
Posttijd: 09-dec-2024